Najczęstsze awarie wtryskarek spowodowane niepoprawnym doborem środków smarnych i sposoby ich uniknięcia.
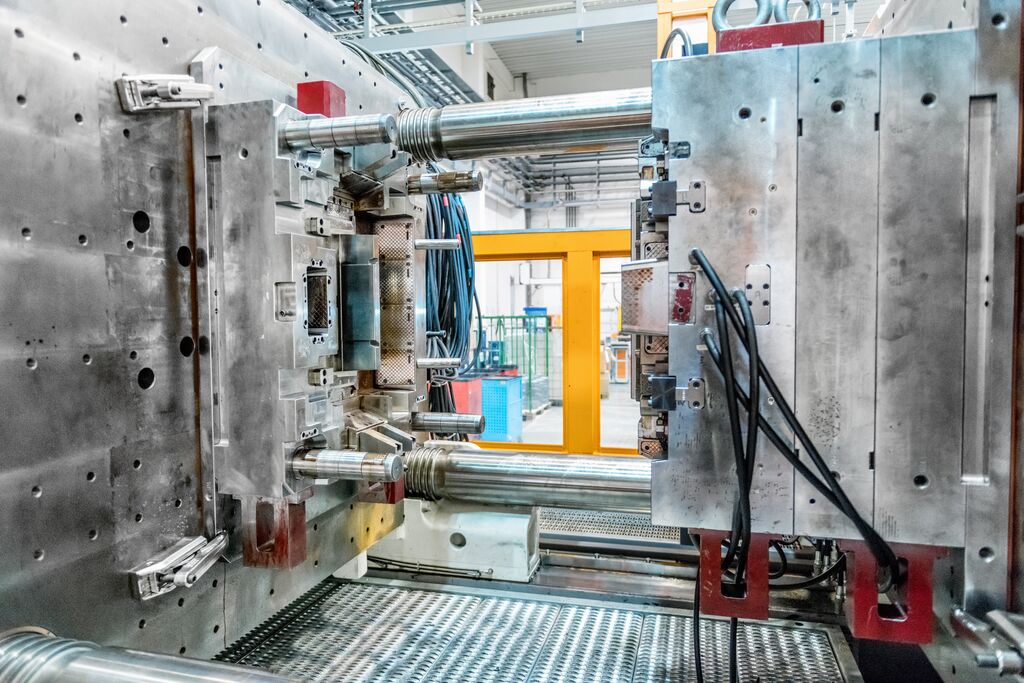
Autorem artykułu jest mgr inż. Piotr Motyka, absolwent Politechniki Wrocławskiej. Ponad 40 lat pracy w przemyśle maszynowym. Konstruktor pierwszych obrabiarek CNC w Polsce.
W celu poprawnej analizy doboru środków smarnych należy dokładnie zapoznać się z przeznaczeniem i budową wtryskarek, czyli obrabiarek do formowania wtryskowego tworzyw sztucznych. Jest wiele typów wtryskarek, ale najbardziej podstawowy podział obejmuje tym czynnika roboczego. W tym podziale wyróżniamy wtryskarki hydrauliczne gdzie w układzie napędowym tłoczony jest pod wysokim ciśnieniem olej hydrauliczny oraz wtryskarki elektryczne gdzie czynnikiem napędowym jest silnik elektryczny. W przemyśle zdecydowanie dominują wtryskarki hydrauliczne zapewniające ciągłość pracy przy dużym obciążeniu w zmiennych warunkach pracy, dające możliwość produkcji elementów wielkogabarytowych. Wtryskarki elektryczne stosowane są głównie w produkcji elementów małogabarytowych. Pozwalają na uzyskanie elementów precyzyjnych z dużą dokładnością wymiarową.
Podstawą niezawodnej i długotrwałej pracy wtryskarek hydraulicznych jest właściwy dobór oleju hydraulicznego stanowiącego podstawowy element transmisji mocy. Ma to bezpośredni wpływ na wydłużenie czasu eksploatacji, zmniejszenie awarii i nieplanowanych przestojów jak również na wzrost wydajności, a tym samym na osiągnięcie znacznych efektów ekonomicznych. Większość wtryskarek i tzw. wydmuchiwarek przemysłowych jest przystosowana do pracy na olejach hydraulicznych o lepkości kinematycznej 46 i 68 cSt. Zdecydowaną przewagę mają wtryskarki pracujące z zastosowaniem oleju o lepkości kinematycznej 46 cSt (mm2/s) wyznaczonej laboratoryjnie w temp. 40 oC. Olej taki powinien posiadać wysoki wskaźnik lepkości, odporność na degradację termiczną i chemiczną, stabilność w obecności wody, powinien zawierać dodatki antykorozyjne oraz wiskozatory i depresatory czyli polimery, które stabilizują lekkość i pozostałe parametry fizyko-chemiczne przy zmianie temperatury. Ma to istotny wpływ na tzw. pompowalność oleju i utrzymywanie prawidłowej warstwy filmu smarnego. Dzięki temu w znacznym stopniu zmniejsza się zużycie mechanizmów tnących, a tym samym zwiększa się żywotność elementów ruchomych wtryskarki. Duże znaczenie mają również dyspersanty zawarte w oleju.
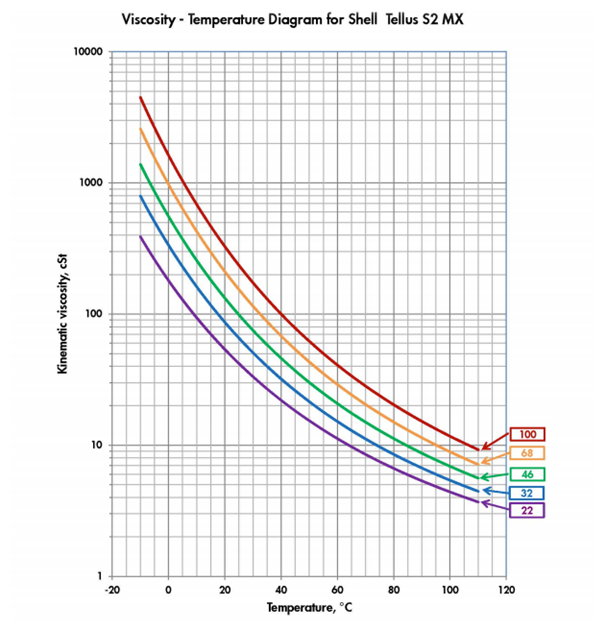
Wpływają one na niwelowanie cząstek stałych co zmniejsza siłę tarcia i zwiększa filtrowalność eliminując zjawisko ?stick-slip?, a tym samym na likwidację drgań i zużycie łożysk tocznych i ślizgowych. Jest wiele olejów hydraulicznych różnych producentów, które gwarantują uzyskanie opisanych efektów. Jednym z nich jest olej produkowany przez firmę Shell o nazwie Tellus S2 MX 46 oraz Tellus S2 MX 68. Olej ten o dwóch rodzajach lepkości kinematycznej spełnia wysokie wymagania stawiane przez najnowszej generacji systemy hydrauliczne. Dzięki zawartości dyspersantów, olej ten posiada bardzo dobrą filtrowalność, utrzymuje separacje wody, uwalnia pęcherzyki powietrza co zapewnia dużą odporność na pienienie, a tym samym zwiększa sprawność systemów hydraulicznych. Należy podkreślić, że wtryskarki z reguły pracują w pomieszczeniach zamkniętych co gwarantuje stabilność temperatury otoczenia. W zależności od typu wtryskarki, gabarytu produkowanych elementów i średnicy siłowników hydraulicznych, temperatura pracy oleju hydraulicznego zawiera się w granicach 35oC do 55oC. W tylnej końcowej części wtryskarki znajduje się stabilna nieruchoma płyta, do której w czasie wtrysku dociskana jest forma poprzez ruch płyty ruchomej przesuwanej po kolumnach prowadzących lub po prowadnicach zamontowanych na łożu korpusu wtryskarki. W dużych wtryskarkach przy sile zacisku 10 000 kW (1kN = 101,97kG) wymagających siłowników o dużych średnicach musi być zainstalowany sprawny system chłodzenia oleju hydraulicznego, aby zachować temperaturę pracy oleju w przedziale przewidzianym przez producenta. Na zamieszczonym wykresie widzimy przebieg zmiany lepkości kinematycznej oleju Shell Tellus S2 MX w funkcji temperatury. Dwa rodzaje oleju o lepkościach 46 cSt i 68 cSt mieszczą się z utrzymaniem właściwej lepkości w obrębie temperatury pracy wtryskarek.
Obok oleju ważnym czynnikiem gwarantującym niezawodną pracę wtryskarek są smary, zwłaszcza przy zastosowaniu do łożysk silników elektrycznych napędzających przekładnie ślimakową podającą rozgrzany granulat przetwarzanego plastomeru. Najlepsze w tym przypadku są smary syntetyczne o zwiększonej trwałości do łożysk wysokoobrotowych. Smar taki powinien być odporny na wypływanie przy zwiększonej temperaturze. W tym przypadku zalecane są smary o gęstości w klasie wg NLGI 2,5 lub 3. Firma Shell zapewnia prawidłowe smarowanie poprzez zastosowanie smaru o zagęszczeniu litowym (Li). Smar ten jest w pełni syntetyczny o nazwie Shell Gadus S5 V42P 2,5 w klasie NLGI 2,5. Jest on w szczególności zalecany do łożysk silników elektrycznych zamontowanych we wtryskarkach. Układ smarowania podajników surowca we wtryskarkach, wydmuchiwarkach i wytłaczarkach jest taki sam. Nowe generacje tych maszyn zwiększają wymogi jakości smaru i z tego względu coraz większe zastosowanie mają smary zagęszczone kompleksowym sulfonianem wapnia, dającym wysoką wytrzymałość na duże obciążenia mechaniczne i wysoką temperaturę kroplenia powyżej 300oC. Wtryskarki konstruowane są pod kątem wymogów produkcyjnych. Można jednak przedstawić ogólny schemat budowy, który obrazuje potrzebę zastosowania różnych środków smarnych.
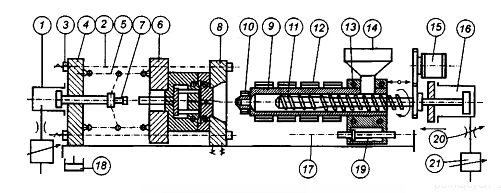
Jak widzimy na tym schemacie ślimak obraca się w cylindrze, który jest podgrzewany w celu wstępnego uplastycznienia tworzywa jakim jest granulat podawany z leja zasypowego. Ślimak poprzez ruch obrotowy przesuwa tworzywo w cylindrze i jednocześnie miesza to tworzywo co powoduje równomierne ogrzewanie granulatu. Czynnikiem ogrzewającym ślimak są elektryczne elementy grzejne wbudowane w płaszczu wtryskarki.
Jest jednak wiele rozwiązań, które zamiast bezpośredniego zasypu granulatu, dostarczają wstępnie podgrzane tworzywo z osobnego zasobnika. Podgrzewanie to następuje w wyniku transmisji ciepła oleju grzewczego będącego w wymuszonej cyrkulacji za pomocą oleju grzewczego (np. Shell Heat Transfer Oil S2). Olej grzewczy powinien być w wysokim stopniu odporny na proces krakingu, utlenianie i zmianę lepkości. Najważniejszą cechą w tym przypadku jest niewielka ilość lotnych związków, które mają niską prężność co zabezpiecza oleje przed procesem krakingu. Jest to bardzo ważny proces w przypadku olejów grzewczych, który polega na rozpadzie dłuższych łańcuchów alkanów na krótsze alkany i alkeny. Należy podkreślić, że kraking następuje na skutek działania wysokiej temperatury.
Reakcje chemiczne zachodzące w czasie krakingu sprowadzają się do pękania pojedynczych wiązań chemicznych węgiel-węgiel z wytworzeniem wolnych rodników, które inicjują powstanie metanu, gazu LPG, nienasyconych węglowodorów koksu. Przy spadku temperatury, mieszanina ta zaczyna krystalizować tworząc masę asfaltową będącą ciałem stałym. Proces ten jest nieodwracalny i doprowadza to do trwałego zaślepienia przelotu rur.
W ramach programu wdrażania olejów specjalistycznych firma Shell wprowadziła na rynek olej syntetyczny Shell Tellus S4 VE przeznaczony do wtryskarek tworzyw sztucznych. Olej ten został opracowany na bazie technologii GTL (gas-to-liquid) z myślą o wydłużeniu pracy wtryskarek, a tym samym zmniejszeniem kosztów produkcji. Duże znaczenie ma tutaj wpływ na zmniejszenie zużycia energii elektrycznej i wydłużenie bezawaryjnego czasu pracy wtryskarek. Olej ten cechuje krótszy czas uwalniania powietrza ze zbiorników hydraulicznych co zapewnia ochronę przed tworzeniem się pęcherzyków co zmniejsza hałas, eliminuje pękanie gumowych węży hydraulicznych i zmniejsza awarię pomp.
Analiza awaryjności wtryskarek sprowadza się najczęściej do zespołów ruchomych. Najważniejszy z nich to zespół zamykania i otwierania form. Forma wtryskowa składa się z dwóch płyt z których, jedna jest przymocowana do korpusu wtryskarki, a druga jest przesuwana po kolumnach prowadzących lub po prowadnicach zamontowanych na korpusie wtryskarki. Powierzchnie cierne tych elementów smarowane są przez podajnika smaru. Należy codziennie sprawdzać ilość smaru zawartego w tych pojemnikach. Używamy w tym przypadku smaru powinien być odporny na podwyższone temperatury, powinien być odporny na wysokie naciski EP (Extreme Pressure) oraz posiadać konsystencję NLGI 1,5. Sprawdzone w praktyce i zalecane są tutaj dwa smary Firmy Shell tj. Gadus S5 T460 1,5 oraz Gadus S3 T460 1,5.
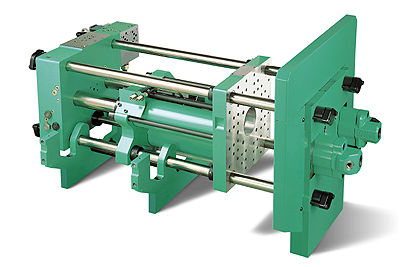
Smary te znakomicie sprawdzają się przy smarowaniu powierzchni kotłów prowadzących wyrzutnika oraz wszelkich innych płaszczyzn ślizgowych. Należy podkreślić, że temperatury robocza oleju hydraulicznego wynosi 45-50oC. Tak więc konsystencja smaru powinna zabezpieczać smarowane elementy przed wpływem smaru, a tym samym zmniejszać ryzyko zatarcia. Wzrost temperatury oleju powyżej 60oC świadczy najczęściej o zbyt małej ilości tego oleju w zbiorniku agregatu zasilającego. W tym przypadku należy bezzwłocznie uzupełnić olej do wymaganego stanu. Jeżeli wokół stanowiska wtryskarki pojawiają się plamy olejowe czyli następuje tzw. zjawisko pocenia wtryskarki to najczęściej przyczyną tego są nieszczelności olejowe, które wystąpiły na skutek zmniejszania lepkości kinetycznej oleju pod wpływem wzrostu temperatury pracy oleju. W tym przypadku należy sprawdzić jakość uszczelek, zmniejszyć temperaturę, a w przypadku mocno wyeksploatowanych wtryskarek przejść na olej o zwiększonej lepkości kinematycznej i większym wskaźniku lepkości. Ma to też istotne znaczenie jeśli wypracowane wtryskarki mają większe luzy robocze, zwiększoną stałą czasową, wycieki, nadprodukcję ciepła, straty energii i gromadzenia się zanieczyszczeń. To wszystko wiąże się z zastosowaniem właściwych środków smarnych. W celu polepszenia warunków pracy wtryskarek, środki smarne powinny posiadać wysoki wskaźnik lepkości, zdolność do filtracji oraz dobrą odporność na utlenianie. Wydłużona żywotność oleju chroni najważniejsze elementy układu hydraulicznego takie jak serwomechanizmy i zawory. Dlatego wydłużenie okresów wymiany oleju, bez ryzyka awarii sprzętu jest możliwe wyłącznie przez zastosowanie wysokości jakości środków smarnych o właściwym pakiecie dodatków uszczelniających.
mgr. inż. Piotr Motyka
Industrial Engineering Manager
Wróć do kategorii: Oleje i smary Wiedza