Powietrze w układzie hydraulicznym
Możliwość komentowania Powietrze w układzie hydraulicznym została wyłączona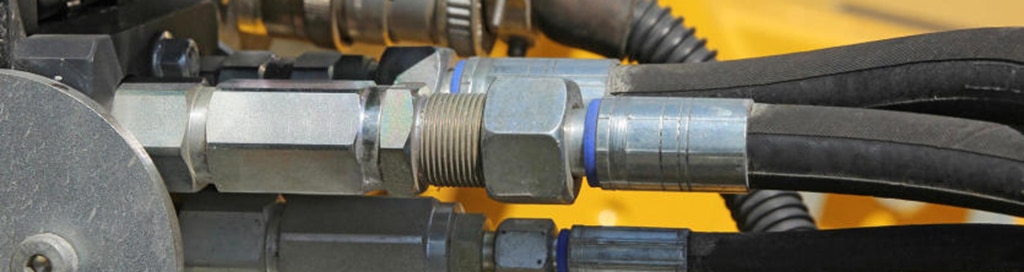
Autorem artykułu jest mgr inż. Piotr Motyka, absolwent Politechniki Wrocławskiej. Ponad 40 lat pracy w przemyśle maszynowym. Konstruktor pierwszych obrabiarek CNC w Polsce.
[latexpage] Zapowietrzone układy hydrauliczne transmisji mocy sprawiają w praktyce bardzo wiele problemów. Wiedza o niedoskonałościach takich systemów może być bezcenna, jeśli weźmie się pod uwagę możliwość uniknięcia awarii, zwiększanie wydajności, zmniejszenie kosztów eksploatacji, a także znaczne wydłużenie żywotności maszyn i urządzeń przy zmniejszonej stałej czasowej przekazu transmisji mocy. Dyspergencja powietrza w oleju nie jest szkodliwa, ale koagulacja tak. Drobne pęcherzyki powietrza pod wpływem ciśnienia i temperatury łączą się, co w konsekwencji doprowadza do powstania dużych pęcherzy powietrza o znacznie większej ściśliwości niż oleju, w którym są tworzone. Ściśliwość objawia się zmianą objętości gazu zachodzącą pod wpływem działania sił powierzchniowych i dla gazów jednoskładnikowych wyraża się wzorem:
\[
{Z} = \frac{PM}{\rho RT}
\]
M ? masa cząsteczkowa gazu
P ? ciśnienie
T ? temperatura
? ? gęstość
Z ? współczynnik ściśliwości gazu
R ? uniwersalna stała gazowa
Tak więc w przypadku powietrza, czyli wieloskładnikowego gazu ściśliwość jest również zależna w dużym stopniu od wielkości ciśnienia i temperatury. Wewnątrz gazu pozostającego w równowadze panuje ciśnienie pochodzące od jego ciężaru właściwego zwane ciśnieniem aerostatycznym, które wyraża się wzorem:
\[
{p} = {h\gamma}
\]
h ? wysokość słupa gazu
?- średni ciężar właściwy gazu
Dla powietrza ciężar właściwy ? w warunkach normalnych wynosi średnio 1,293 G/dcm3.
Górna granica nasycenia powietrza w oleju zależy od ciśnienia. W miejscach, gdzie następuje spadek ciśnienia tworzą się pęcherzyki powietrza. Ma to miejsce najczęściej przy zaworach, cylindrach hydraulicznych, pod uszczelnieniami, w miejscach zakuwania węży gumowych, a także przede wszystkim w miejscach, gdzie pod wpływem ciśnienia następuje zwiększenie średnicy przelotu węży gumowych. Jest to bardzo istotne z uwagi na negatywny efekt końcowy objawiający się pękaniem węży hydraulicznych i niszczeniem uszczelek PTFE. Każdy impuls transmisji mocy powoduje przemieszczanie się drobinowych pęcherzyków powietrza, które w dogodnym dla nich miejscu tworzą koagulację dużej wielkości pęcherza. Tworzenie się pęcherzy o znacznej wielkości jest bardzo niebezpieczne dla trwałości węży hydraulicznych, uszczelnień oraz stabilnej pracy maszyn i urządzeń, a zwłaszcza wtryskarek.
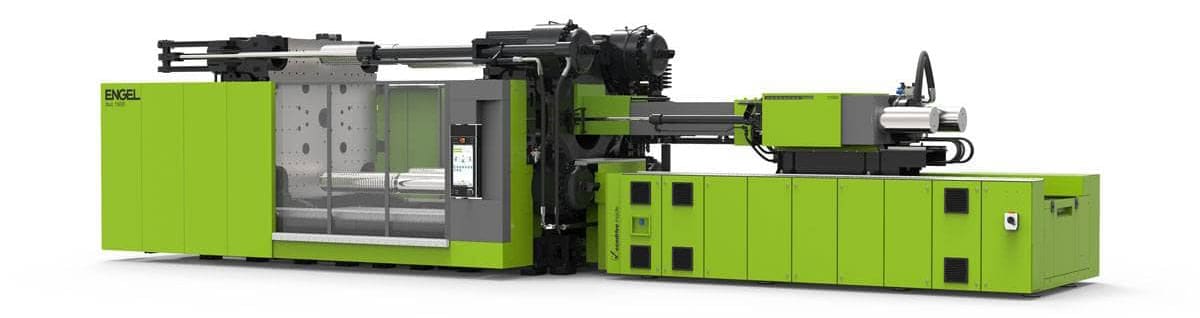
Pod wpływem zmian ciśnienia i temperatury dochodzi wewnątrz pęcherzy powietrza do kawitacji gazowej. Należy tutaj pamiętać o kawitacji zachodzącej w cieczy w obszarach turbulentnych, gdzie przepływ jest wielkością złożoną wielu czynników i stanowi tzw. przepływ wielofazowy, w tym przypadku oleju i powietrza. Jeżeli w obszarze turbulentnym w oleju znajduje się woda to wówczas w procesie kawitacji staje się ona katalizatorem procesu tworzenia pęcherzy powietrza. W wyniku tego działania dochodzi do depresji dynamicznej, czyli lokalnego gwałtownego spadku ciśnienia statycznego prowadzącego do wrzenia drobin wody, które przechodząc w stan gazowy katalizują pęcherze powietrza. W ten sposób tworzy się kawitacja gazowa, która w wyniku dyfuzji gazu znajdującego się w oleju do istniejących już w nim pęcherzyków powietrza wpływa na ich rozrost. Przy impulsach transmisji mocy olej jest cieczą o bardzo małej ściśliwości w stosunku do wytworzonych w nim pęcherzy gazowych, gdzie następuje gwałtowny wzrost ich objętości i ciśnienia. W końcowej fazie tego zjawiska dochodzi do implodowania pęcherzy gazowych objawiając się pękaniem węży gumowych, niszczeniem uszczelek, a także części metalowych maszyn i urządzeń. Jeżeli zapowietrzony olej dotrze do pompy, wówczas nastąpi sprężenie gazu, na skutek którego pompa zmniejszy swoją sprawność. Tak tłoczony olej w drodze transmisji mocy do mechanizmów wykonawczych np. cylindrów siłowników spowoduje to, że układ najpierw będzie musiał sprężyć powietrze, a dopiero później dojdzie do transmisji mocy i tym samym stała czasowej reakcji siłowników będzie znacznie wydłużona.
Zapowietrzony układ hydrauliczny daje o sobie znać w postaci drgań, wibracji i hałasu. W celu zapobiegania zapowietrzenia układu hydraulicznego, należy stosować oleje zaliczane do wyższych klas jakości np. wg norm ISO/DIS 6743 klasy HM i HV. Są to oleje głęboko rafinowane, gdzie obok różnych dodatków uszlachetniających znajdują się inhibitory utleniania, a więc antyoksydanty oraz dodatki antypienne. Należy podkreślić, że większość maszyn i urządzeń w czasie pracy generuje różnego rodzaju drgania, które powodują absorpcję powietrza do oleju. Objawia się to powstawaniem piany w oleju. Na skutek utleniania oleju następuje jego degradacja. Tendencja do tworzenia piany uzależniona jest od napięcia powierzchniowego. Niższa lepkość kinematyczna oraz niższe napięcie powierzchniowe olejów mineralnych w stosunku do olejów syntetycznych utrudnia tworzenie się piany. Wysokie napięcie powierzchniowe olejów syntetycznych stabilizuje proces tworzenia się piany, a powstające pęcherze są bardzo małych rozmiarów. Dodatki antypienne oddziaływają na napięcie powierzchniowe oleju co pozwala na separację pęcherzyków powietrza. Tworzenie się piany w oleju stanowi zagrożenie dla prawidłowej pracy całego układu hydraulicznego i to zarówno o charakterze hydrokinetycznym jak i hydrostatycznym. Wysoka skłonność olejów syntetycznych do tworzenia piany, związana jest z dużym napięciem powierzchniowym tych olejów, a więc z energią przypadającą na jednostkę powierzchni co jest równoważne pracy potrzebnej do powiększenia powierzchni o tę jednostkę. Siły przyciągania między molekułami cieczy są miarą wielkości napięcia powierzchniowego. Hydrauliczne oleje syntetyczne dzięki wysokiemu napięciu faz termodynamicznych utrzymują wysoką wewnętrzną dla każdej fazy kohezję, a więc spójność wewnętrzną, która jest większa od adhezji, czyli siły przylegania na granicy faz termodynamicznych. Napięcie powierzchniowe jest zależne od pracy jaką trzeba wykonać by utworzyć jednostkową powierzchnię cieczy i wyraża się wzorem:
\[
{\gamma} = \frac{\Delta W}{\Delta S} [J/m^2]
\]
? – napięcie powierzchniowe
?W ? praca potrzebna do utworzenia powierzchni ?S
?S ? pole powierzchni
Napięcie powierzchniowe można również wyrazić jako zależność siły do długości odcinka, na którym ta siła działa:
\[
{\gamma} = \frac{F}{L} [N/m]
\]
? – napięcie powierzchniowe
F ? siła napięcia powierzchniowego działająca równolegle do powierzchni cieczy, dążąca do zmniejszenia powierzchni cieczy
L ? długość odcinka, na którym działa siła
Tak więc możemy precyzyjnie zdefiniować, że napięcie powierzchniowe to inaczej siła styczna do powierzchni oleju hydraulicznego, działająca na jednostkę długości obrzeża powierzchni tego oleju. Im większa jest ta siła, tym większa jest odporność oleju do zapowietrzania, a więc przenikania cząstek powietrza do oleju. W termodynamice napięcie powierzchniowe jest wprost proporcjonalne do entalpii swobodnej, a odwrotnie proporcjonalne do wielkości powierzchni i wyraża się wzorem:
\[
{\gamma} = \frac{\partial G}{\partial S}
\]
? – napięcie powierzchniowe międzyfazowe
G – entalpia swobodna (energia Gibbsa)
S – wielkość powierzchni
Napięcie powierzchniowe można zmniejszyć poprzez dodanie substancji powierzchniowo czynnych, czyli surfaktantów takich jak emulgatory czy detergenty. Zmniejszenie surfaktantów w oleju powoduje zwiększenie napięcia powierzchniowego co w efekcie utrudnia dyfuzję cząsteczek powietrza w oleju, a tym samym olej nie wykazuje tendencji do pienienia. W tym celu najczęściej stosuje się środek antypienny ?FoamFree 940? produkowany na bazie jonowych środków powierzchniowo czynnych, bez silikonów i olejów mineralnych. Znany jest też środek antypienny ?CHEDF 9022? produkowany na bazie 20% emulsji silikonowej oraz mieszaniny środków powierzchniowo czynnych.
Reasumując należy jednoznacznie podkreślić, że pienienie będące objawem napowietrzenia wywołuje negatywne skutki w postaci spadku wydajności pomp, wypływania oleju ze zbiorników, pękania gumowych węży i nadmiernego utleniania oleju przyśpieszającego proces starzenia. Lepkość, gęstość i napięcie powierzchniowe charakteryzują skłonność oleju do napowietrzania. Oleje mineralne wykazują znacznie mniejszą skłonność do napowietrzania w stosunku do olejów syntetycznych. Poprzez dodawanie do oleju dodatków silikonowych znacznie obniżamy skłonność do napowietrzania, a tym samym do pienienia. Pomiar skłonności wyrażony jest w tzw. Trzech sekwencjach. Każda sekwencja ogranicza się do ściśle wyznaczonej temperatury pomiaru. Sekwencja pierwsza w temperaturze 25oC, sekwencja druga w temperaturze 95oC i sekwencja trzecia w temperaturze 25oC, ale po próbie w temperaturze 95oC. W każdej sekwencji wynik pomiaru przedstawiony jest w postaci dwóch liczb np. 15/0. Pierwsza liczba określa tendencję do pienienia w mililitrach, natomiast druga trwałość piany w mililitrach w określonym normą czasie. Należy pamiętać, że intensywne napowietrzanie zawsze wywołuje pienienie. Detergenty, inhibitory korozji, wiskozatory itp. dodatki zmniejszają napięcie powierzchniowe oleju. Pienienie oleju często wywołuję kawitację. Dodatki uszlachetniające powodują powstanie na powierzchni oleju cienką warstwę antypienną. W tym przypadku najsilniej działają dodatki na bazie silikonu. Pęcherzyki powietrza pękają pod wpływem działania mikro kropelek silikonu. Należy podkreślić, że działanie to jest tylko skuteczne w takich olejach, których baza olejowa nie rozpuszcza sylikonu, a więc przede wszystkim w olejach mineralnych. Tam, gdzie nie można ze względów eksploatacyjnych zastosować sylikonu stosuje się glikole i estry fosforanowe.
Kończąc, należy dokładnie przeanalizować dobór oleju do maszyn i urządzeń, a w szczególności do wtryskarek, gdzie niezawodność pracy, trwałość gumowych węży hydraulicznych oraz niski poziom stałej czasowej poszczególnych cykli pracy przekłada się na wydajność, a tym samym na wymierne korzyści finansowe.
mgr. inż. Piotr Motyka
Industrial Engineering Manager